We are
still alive, just, and are here on Leros, in Partheni Boat
Yard.
Right,
we arrived here on the 2nd June and were lifted
straight out of the water and onto the “hard”. The boat
yard is right by a military base, so no ‘photos are allowed
except in the yard.
The
main jobs to be carried out were;
1.
Scrape the bottom of the boat,
repaint and re antifoul
2.
Have the engine cylinder head
“looked at”.
3.
Have a new exhaust system
fitted.
4.
Renew the cutlass and stern
gland bearings on the propeller shaft. The cutlass bearing
is the last bearing before the prop itself and in always
underwater, the stern gland is the bearing / seal that stops
the water coming into the boat!
Straight into it, off with the propeller!
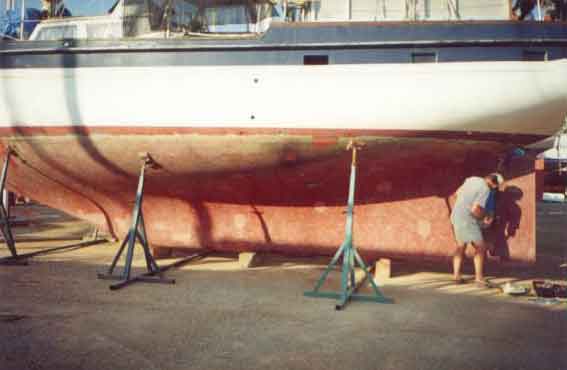
During this operation, I found that the
cutlass bearing was well shot. There was about ¼ inch of
play in the bearing! The
next morning we started scraping the hull, what a job!
Several years of antifoul, some grotty paint to be removed.
As with all scraping jobs on Mandarina, small is beautiful.
A ½ and ¾ inch chisel being the preferred implements…..
The underwater section of the hull is bl**dy huge.
It took us 21 days to scrape all the cr*p off the bottom!
That’s every day for 21 days, with one day off! With both
of us scraping! The boat
yard is miles from everywhere (except the army camp and one
excellent taverna), so I scrounged the use of a moped from
Stein, a Norwegian neighbour, to get some essential supplies
from the local shop (beer, retsina fags etc…..)
The Yard Manager, Angelo, arranged for us to have a meeting
with Michaelis, the Technical manager, on Tuesday 5th June.
Michaelis, or the Maestro, as he is known, chooses not to
speak much English, not because that he is rude, but he is
in fact shy of not speaking it correctly!
A program of work was planned, the head was to come off, a
new exhaust system designed and fitted, and the prop shaft
removed for inspection and bearing replacement.
With a view to all this I cleared the engine room to enable
work to commence, and Caz cleared out all the lockers that
the existing exhaust pipe went through.
As
an aside, all the other members of the boat yard community
offered us various scrapers and sanding devices, all to no
avail. The cra*p on our boat resisted all except the
faithful chisels.
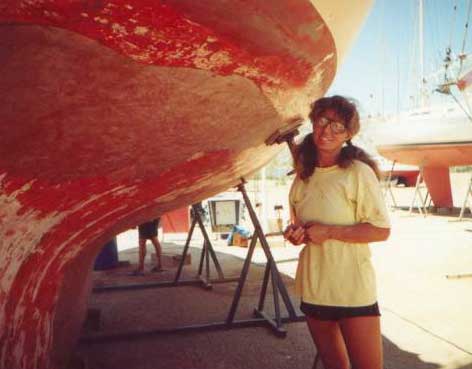
The hull
had dried out by Thursday, and I had noticed that a previous
repair to the rudder had failed and had let water into the
foam filled cavity of the rudder. I drilled drain holes,
let it dry out and repaired “properly” with epoxy filler.
The port
side of the boat was scraped by 11th June. The cylinder
head and old exhaust were removed on 12th June.
The head
was a right state. Well clagged up with goo, gunge and
crud. This was caused by too much back pressure through the
old exhaust system. The “old” system went up from the
exhaust manifold, about a metre!, in a stainless silencer.
Cooling water was injected at the top (to silence and to
cool the exhaust gases), the gases and water then dropped
down a metre to the engine room floor in a flexible hose.
The hose then went up over a metre, through the cockpit
locker, through the aft head locker, through all the lockers
in the port side of the aft cabin, finally exiting at the
back of the boat. The tubing length was over 14 meters long
when I measured it…….
While
scraping the starboard side we came across a redundant echo
sounder transponder, set in teak, attached to the hull. Off
it came and the holes filled with epoxy filler.
June 14th
saw the removal of the prop shaft. Not a pretty sight, in
fact beyond repair! The was a huge area of wear adjacent to
the stern gland that was due to the crap packing that I
removed about a year ago. The shaft (three meters long, 1 ¾
“ diameter) was not replaceable, so The Maestro said that he
would make a new one for us! Drachma before the eyes!
As Stein
had now left the yard I hired a moped and on Saturday 16th
June we set off to Lakki, the main town on Leros, to
purchase a electric sander to sand the hull. I bought 2 x 5
meters of sanding paper as well, one coarse, one fine.
The
Maestro summoned me to the workshops on 19th June to inspect
the testing of the fuel injectors. All were fine (and they
should have been as they were only replaced late last
year!). The head was declared fit for overhaul, so the
valve seats were re-cut, new valves and springs fitted and a
general clean up of the ports completed.
Sunday
24th June saw the end of the sanding of the hull, hooray!
The next
job was to prime the hull ready for antifouling. As the
head, exhaust and shaft were nowhere to be seen, I decided
to paint the top sides of the hull while the boat was out of
the water.
More
sanding, delightful!!
Caz had
been busy making wind awnings for the cockpit sides, and
very posh they are as well. They will also keep the rain
off us if a shower should arrive.
27th June
arrived and I took down the two plaques from the back of the
boat, the “Mandarina” and the “London” timber work needing a
good seeing to.
The
“London” sign on the plaque had only been painted, so I
decided to carefully route out the letters, making them
match the Mandarina plaque.
The
Mandarina plaque was in a bad state of repair. There were
splits and cracks in the carvings. I repaired the cracks
and splits by gluing them together and then screwing them
together with stainless steel screws to add strength. Caz
undercoated both the lumps of wood, especially the backs,
which had not been touched from new!
29th June
saw the shaft back in the hull, new cutlass bearing fitted
etc. 30th June saw the head
back on the engine!
2nd July saw the name plaques both painted blue, on
top of three coats of two pack epoxy undercoat.
The hull had now received six
coats of two part epoxy primer, yes that’s six coats, the
minimum to ensure that the hull will remain waterproof.
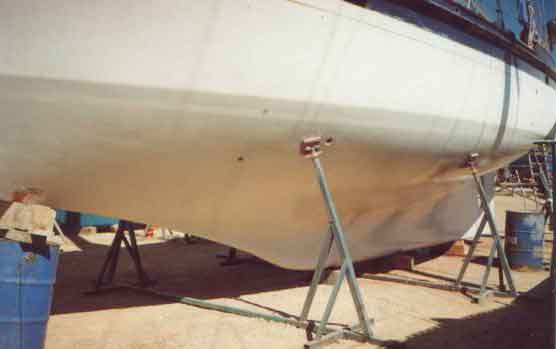
A coat of
“hard” anti foul was then added. This will mean that we can
revert to hard antifoul in the future. (See below).
The hole
that the old exhaust went out of the back of the boat was
filled, very expertly, by the yard’s glass fibre specialist.
The next
day I “picked” out the letters on the name plaques in white,
three coats, with a tiny brush, knackering. I also repaired
the aft section of the starboard rubbing strake that had
been savaged during last year. A lump of “left over” teak
from a previous repair being let into the existing timber.
Caz had
been making new loose covers, recovering the life buoys, and
having a mega-polish of all the bright work on deck. She
had also decided to repair a split in the mizzen sail and
also to renew the sacrificial strip (to stop UV degradation
of the sail). This meant that she had to use the bosun’s
chair!
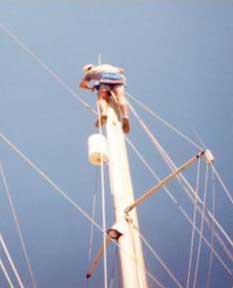
The new
exhaust had now been designed, a much neater system, with a
custom made water cooled manifold, silencer and waterlock.
The gases and water now exit out of the side of the boat.
This saves about 10 meters of exhaust tubing!
I decided to follow Caz’s example and also went up the
mizzen mast to remove the redundant radar dome, redundant
SatNav aerial and to tighten the VHF aerial.
5th July saw the start of the undercoating of the topsides.
Only two coats this time.
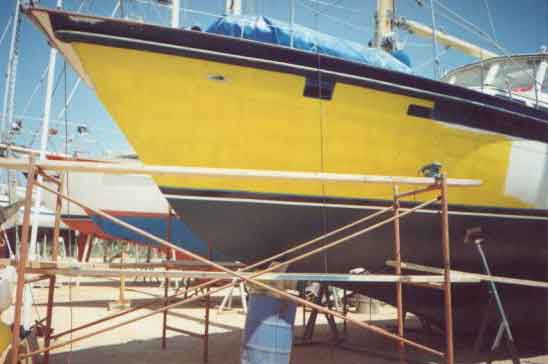
The
attractive yellow is a chemical etch primer, not a change of
boat colour! The yellow was covered by a grey, two part
epoxy, then three coats of white. The “old” 8 mm anchor
chain has been replaced with 100 metres of 10 mm.
You might also spot that we now have a “boot strap”
line around the hull, a wide blue and a narrow white strip
round the boat. 9th July,
and a beautiful calm hot day. I decided a good day to go up
the main mast to change / renew the navigation light bulbs.
What joy. I don’t mind heights, it’s just a fear of
falling……
Being a
belt and braces sort of chap, I went up on the spinnaker
halyard, with the topping lift as a safety line. The
spinnaker halyard is long enough to reach the anchor winch,
which means that Caz could winch me up with ease.
All went to plan, until I was half way up. The
spinnaker halyard “jumped” out of the pulley at the top of
the mast and jammed! I was half way up, and stuck solid.
Thanks to the topping lift I was able to get down in a
controlled manner! But the spinnaker halyard was stuck
fast. Poo! There was
nothing for it, I had to go up again on the topping lift,
with Caz winching me up by hand!
I got to the top, freed the spinnaker halyard and
quickly attached it as a safety line. The pulley had seized
solid so that had to be freed.
I replaced the bulbs, and checked them before coming
down again!
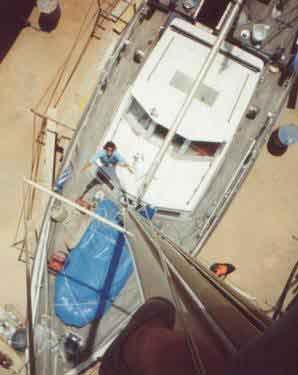
A long
way down! But at least Caz would catch me if I fell
11th July, and the top sides
were complete. And very fine it looks too.
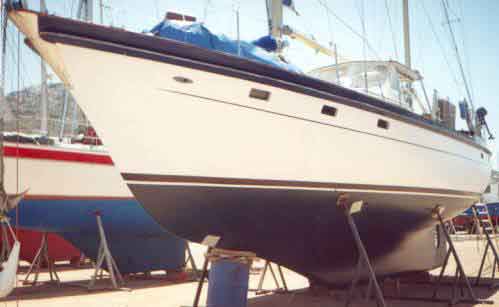
I also
painted the coach line blue, which we think sets everything
off.
The stern looks good too,
with the repainted plaques and the repair finished to the
rubbing strake. (You can’t see the join!).
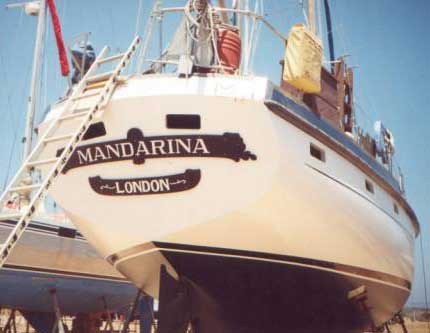
I got the
lads in the yard to move the frame work supports so I could
scrape, prime and anti foul the patches that they had
covered. I also fitted stainless steel plates to reduce
future wear on the top of the stern section, (for the kedge
etc.)
Friday,
13th July, and Maestro and the gang came for a final fiddle
with the engine before running it! After bleeding the
diesel system, it started! No blue smoke, and much
quieter. Phew, not my choice of day for doing such a job……
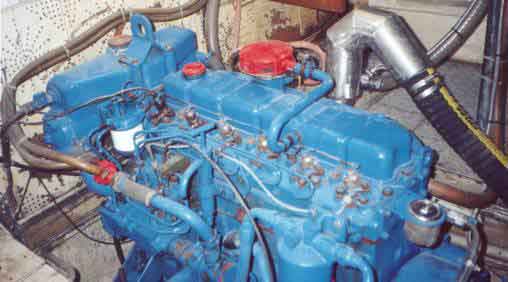
I put the
final three coats of self polishing antifoul on the hull.
This stuff comes off very slowly, as the boat progresses
through the water. It means we won’t be scraping ever
again, as the next time we come out of the water, the old
antifoul can be power washed off.
All that
was left now was to re-stow all the bits and pieces in the
engine room, get the fenders out and get ready to go back in
the water on MONDAY! At last! Oh! And I had to pay the
bill. Ahem. A small consideration.
The bill
included all the antifouling, paint, labour, materials,
exhaust system, head work, new shaft etc. etc. etc. so it
wasn’t so bad.
So, a
very tiring six and a bit weeks. We think that it has been
worth it.
Will be
in touch again soon, I promise!
Jerry
Flint & Carolyn Edwards |